Production of foam products in the company "EMPI-PROM" LLC
Molding machines
The molding machine is designed for sheet foam. The machines manufactured by us are characterized by high quality and reliability. The technology used is the best solutions of Austrian, Italian and South Korean engineers.
The whole process is fully automated.
The operator only adjusts the parameters depending on the brand of the produced material.
We produce two standard sizes of molds 0.5 m 3 and 1.0 m 3 .


Foamer
The foaming agent is used to transfer the initial expanded polystyrene of a given bulk density. The process takes place in a chamber, with intense mixing, where hot steam is supplied. Supply of raw materials and unloading of finished products occurs continuously. The temperature is controlled automatically according to the set parameters. The speed of feed of raw materials is regulated by the operator.
Bulk weight can vary from 12 to 40 kg/m 3 .
With repeated foaming, the weight can be reduced to 7-8 kg/m 3 .
After foaming, the raw material undergoes a drying stage in a fluidized bed dryer.
We produce foamers with a capacity of 50 to 500 kg/hour.
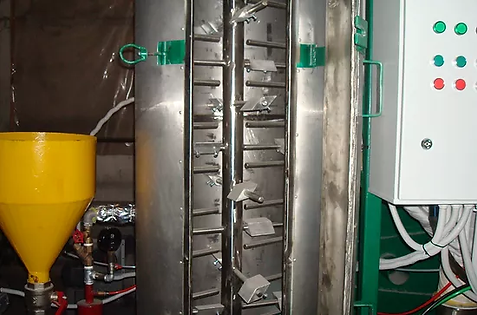

Model equipment used for LGM
The technology of manufacturing models can be divided into the main stages:
foaming and drying of granulated polystyrene is carried out in special equipment - pre-foamers, where the granules are foamed to a certain density, and then enter a drying cabinet, where they completely dry and cool. Next, the polystyrene enters the bunker for storage and oxygen enrichment via the pneumatic pipeline;
production of polystyrene models - autoclaves are used to obtain small, small-batch products - automatic devices where the production of models from expanded polystyrene in metal molds is performed under the influence of pressure. Removal of models from molds, as well as assembly work, is performed manually by the operator. For the production of large-sized parts, model machines are used, which allow to increase productivity up to 4 times;
gluing and painting polystyrene models - ready-made models are assembled into blocks (glued) and treated with a non-stick coating, dipping them in a bath with paint, and then drying;
forming blocks of models in a furnace - for these purposes, a foundry furnace is used - a steel box in which the walls and bottom are equipped with vacuum wires for uniform discharge. The painted model block is placed in the center of the furnace so that the distance to the walls is approximately 50-70 mm and covered with sand. Then the pile is placed on a vibrating table, where with the help of motors, the sand cushion is compacted, prevailing in all planes. Then it is covered with a film, sprinkled with sand and connected to a vacuum apparatus to give the molding sand the necessary strength, as well as to ensure the removal of gases (products of thermal destruction);
casting of the model – molten metal (alloy) is poured directly into the casting mold. It dissolves polystyrene and takes its place, and it repeats the configuration of the model block as accurately as possible;
removal of the finished (cold) casting - the filled blocks of the models are kept in the sand mold from 5-10 minutes to 2-5 hours (the time depends on the technical specifications of the production, the weight of the product and the thickness of the metal). After complete cooling, they are removed and the remains of the non-stick coating are removed.
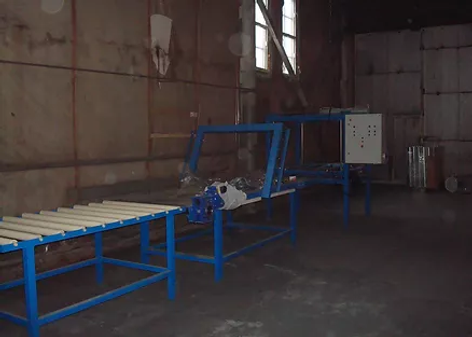
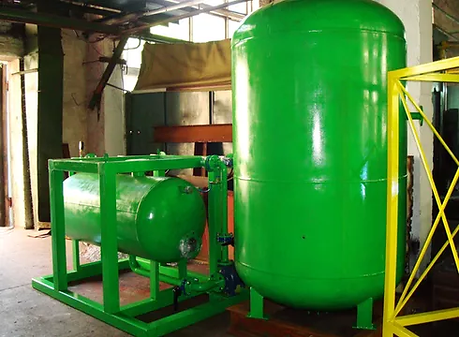